How to Achieve Supply Chain Resilience and Drive Operational Innovation
Supply chains today face pressures from geopolitical instability, pandemics, and extreme weather events. Businesses must navigate uncertainties while ensuring timely deliveries, maintaining quality, and reducing costs. Achieving supply chain resilience enables companies to adapt quickly to disruptions, sustain operations, and drive innovation. This article examines key strategies for enhancing resilience, improving operational efficiency, enabling digital transformation, and integrating innovative logistics solutions. We address each aspect in a question-and-answer format, providing detailed explanations, examples, and industry benchmarks to assist professionals in implementing robust, sustainable strategies.
What Is Supply Chain Resilience and Why Is It Critical Today?
Supply chain resilience is the capability to prepare for unexpected events, respond to disruptions, and recover to a desirable state swiftly. Global supply chains are interconnected and face risks such as natural disasters, pandemics, regulatory changes, and cyberattacks. Companies with high resilience typically experience about 25% less downtime during crises.
Resilience depends on structural flexibility, agile decision-making, and proactive risk management. Multinational corporations use diversified sourcing, redundant logistics networks, and robust IT systems to enhance resilience. For example, predictive analytics and real-time monitoring can improve demand forecasting accuracy by up to 30%, allowing timely adjustments. Embedding safety stock, strategic buffers, and flexible partner contracts also protects revenue and maintains customer trust while supporting ongoing innovation.
How Does Supply Chain Risk Management Prevent Disruptions?
Risk management identifies, assesses, and mitigates potential issues before they become costly disruptions. By evaluating vulnerabilities in production, transportation, and distribution, companies can shield operations from internal and external shocks. Regular monitoring of key performance indicators and using predictive models and scenario planning tools help anticipate risks.
For example, analyzing supplier reliability through on-time delivery percentages and quality defect rates can reduce exposure by nearly 20%. Frameworks inspired by standards like ISO 31000 create a cycle of continuous improvement. This systematic approach prevents disruptions and speeds recovery when events occur.
What Role Does Supply Chain Visibility Play in Building Resilience?
Supply chain visibility means tracking materials and products throughout the entire lifecycle—from suppliers to end consumers. Technologies like RFID, GPS-enabled fleet management, cloud dashboards, and IoT sensors facilitate real-time updates that help quickly identify bottlenecks or anomalies.
Real-time alerts on logistics delays or quality issues enable companies to act within hours rather than days, reducing downtime and protecting revenue. Firms with full visibility report 15–30% fewer production disruptions, as transparency helps optimize inventory and enhances collaboration with suppliers and logistics partners.
How Do Agile Supply Chain Practices Enhance Operational Flexibility?
Agile practices allow rapid adjustment of strategies, resource allocation, and logistics during unforeseen events. Emphasizing short decision cycles and cross-functional collaboration, agile methods enable quick responses. For example, just-in-time (JIT) delivery combined with advanced analytics helps recalibrate schedules on the fly and mitigates the bullwhip effect—reducing its impact by about 22%.
Regular simulation exercises and scenario planning foster a resilient mindset. An agile supply chain not only meets customer expectations with consistent delivery performance but also positions companies to seize emerging opportunities during challenging times.
Which operational efficiency strategies improve supply chain performance?
Operational efficiency is enhanced by integrating process optimization, resource allocation, and technology. Streamlined workflows reduce costs while improving service levels. Emphasis on predictive analytics, process automation, and systematic inventory controls can deliver higher returns on investment and operational gains.
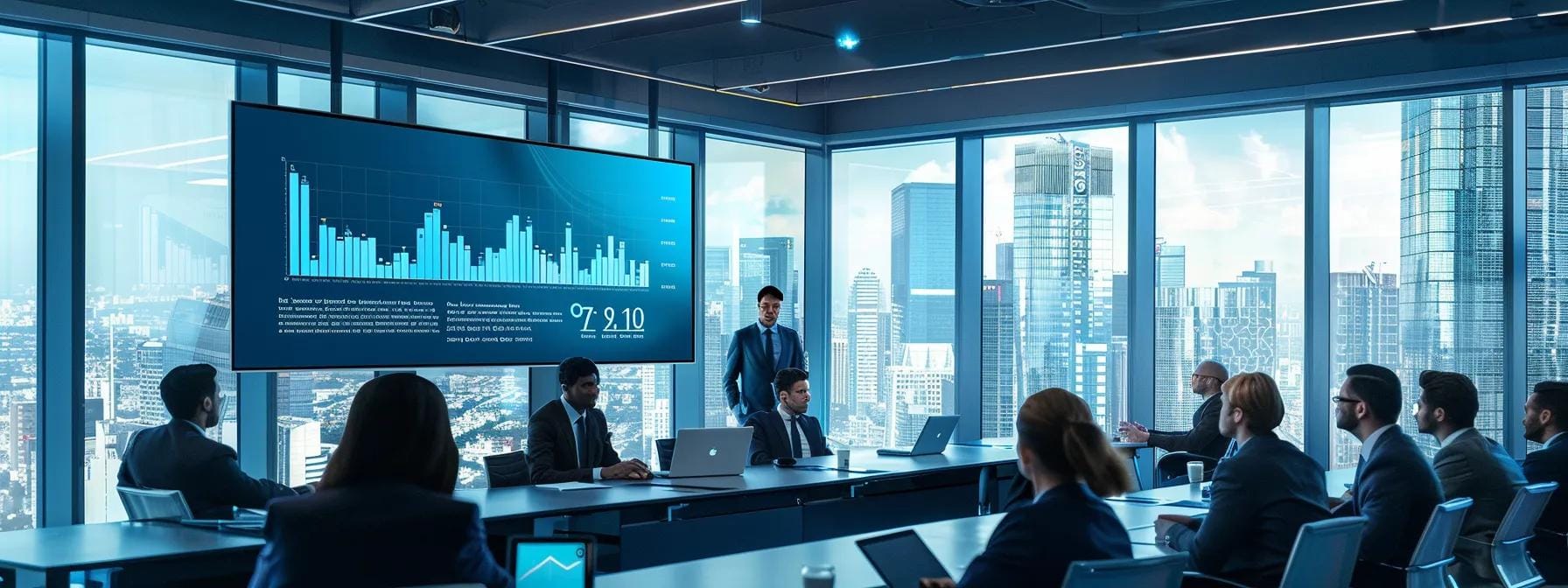
How Can AI and Automation Optimize Supply Chain Operations?
AI and automation are transforming supply chain operations by analyzing large datasets to predict demand patterns, optimize routing, and manage inventory. In warehousing, transportation, and order fulfillment, automation speeds up physical processes and minimizes human error. For instance, coupling AI algorithms with robotics can boost order processing speeds by up to 40%.
Systems that monitor key metrics like lead times and transit delays enable proactive adjustments. Automated decision support systems help balance workloads and adjust pricing in response to market changes, reducing bottlenecks and driving cost savings while improving responsiveness.
What Are Best Practices for Inventory Management and Demand Forecasting?
Effective inventory management and forecasting rely on advanced statistical models that integrate historical data, seasonal trends, and market variables. Techniques such as economic order quantity (EOQ), safety stock calculations, and periodic reviews help maintain optimal stock levels without excessive storage costs.
Companies have improved inventory turnover rates by as much as 35% and reduced stockouts by 20% using these methods. Collaborative initiatives like CPFR between suppliers and retailers further enhance forecasting accuracy. Cloud-based inventory management systems enable real-time data sharing and centralized control, ensuring that inventory aligns with market demand while minimizing obsolescence.
How Does Scenario Planning Support Operational Decision-Making?
Scenario planning involves mapping “what-if” scenarios to anticipate disruptions and identify the best responses. By simulating various conditions—such as spikes in raw material costs or factory shutdowns—companies can uncover vulnerabilities and create detailed contingency plans.
These exercises help prioritize investments in risk mitigation, such as alternative sourcing or buffer stocks. Studies show that effective scenario planning can reduce recovery time by up to 40%, empowering businesses to allocate resources more efficiently in a crisis.
How Does Digital Transformation Enable Supply Chain Innovation?
Digital transformation reengineers traditional supply chain processes by adopting integrated digital platforms, data analytics, and cloud computing. This shift is crucial not only for better disruption response but also for capturing new opportunities that improve customer experiences and operational efficiency.
What Are the Key Components of a Digital Supply Chain Platform?
A robust digital platform integrates various technology layers to offer end-to-end visibility, real-time decision support, and analytics. Key components typically include an ERP system for centralized data, a transportation management system (TMS) for logistics optimization, and a warehouse management system (WMS) for streamlined inventory handling. Additional elements, such as cloud storage, IoT sensors for tracking, and machine learning analytics, further enhance platform capabilities.
For example, integrating IoT with cloud processing can reduce shipment spoilage or damage by up to 15%. Interoperability between these systems breaks down silos and supports swift market responses, while advanced security features like blockchain add traceability and transaction security.
How Can Data-Driven Insights Improve Supply Chain Risk Assessment?
Data-driven insights are fundamental to modern risk assessment. By leveraging big data, companies can monitor trends, detect anomalies, and predict risks well before they escalate. Predictive analytics and machine learning models allow for a detailed analysis of both historical and current events.
For instance, a 20% increase in supplier delays due to adverse weather might trigger immediate corrective actions. Data dashboards that consolidate supplier performance, order accuracy, and inventory levels provide continuous risk monitoring, enabling a proactive rather than reactive management approach.
What Are the Benefits of Integrating Supply Chain Software Solutions?
Integrated supply chain software solutions automate processes, enhance visibility, and allow for real-time stakeholder collaboration. Ranging from ERP systems to specialized logistics tools, these solutions create a fully connected environment that streamlines operations.
Companies using integrated systems often see a reduction in operational costs of around 25% and improve processing times dramatically. By aggregating data into a single view, businesses can quickly identify inefficiencies, optimize routes, and balance inventory—all while ensuring compliance with regulatory standards through automated reporting.
What Innovative Logistics Solutions Support Supply Chain Resilience?
Innovative logistics solutions transform traditional distribution networks into agile, technology-driven systems. By leveraging digital tools, automation, and data analytics, these solutions manage risk, adapt to external pressures, and optimize performance. Whether through real-time tracking or sustainable practices, modern logistics is key to maintaining robust supply chains.
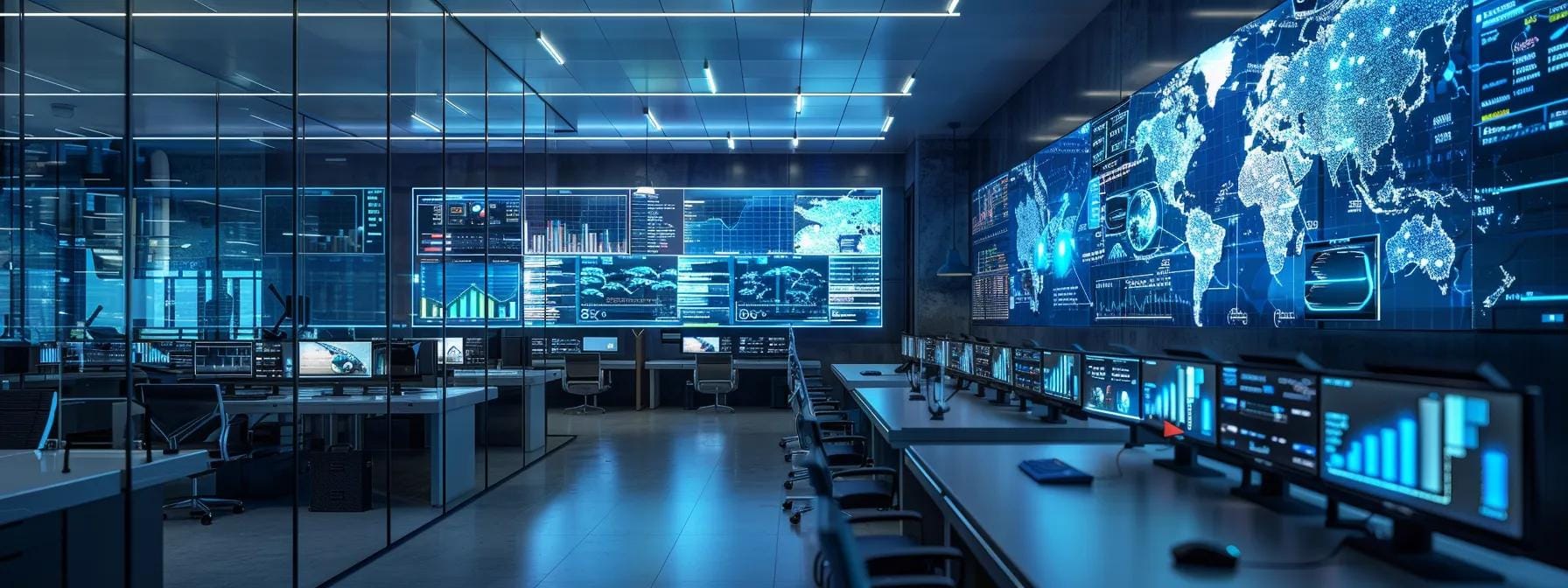
How Do Real-Time Monitoring and Predictive Analytics Reduce Disruptions?
Combining real-time monitoring with predictive analytics minimizes disruptions by continuously tracking shipments and inventory through sensors, GPS, and RFID tags. These systems detect issues early and forecast challenges using historical benchmarks, enabling companies to reallocate resources or adjust delivery routes before minor problems escalate.
For example, detecting traffic congestion or weather anomalies can prompt immediate schedule adjustments, leading to a reduction in delays by about 30%. Early identification of equipment failures or quality issues ensures timely corrective actions and enhanced operational continuity.
What Are Examples of Customizable Logistics Strategies?
Customizable logistics strategies provide tailored solutions for different industries and regions. Multi-modal transportation models, which may integrate trucks, trains, ships, and even drones, offer cost-effective and timely delivery options. Often, companies adopt a hybrid model combining in-house logistics with third-party support to spread risk and leverage specialized expertise.
For instance, a food distributor might use refrigerated trucks alongside on-demand courier services for last-mile deliveries. Reconfigurable warehousing networks demonstrate the flexibility required to sustain consistent service levels in the face of external disruptions.
How Does Sustainability Factor Into Modern Logistics Innovation?
Sustainability is now a central focus in logistics. Sustainable practices optimize transportation routes, employ energy-efficient vehicles, and use eco-friendly packaging to lower the carbon footprint. These initiatives improve efficiency and meet regulatory standards and enhance brand reputation among environmentally conscious consumers.
For example, green logistics strategies can reduce fuel costs by around 20% while improving sustainability ratings. The use of renewable energy sources in warehouses and electric fleets supports cost savings and positions logistics centers as hubs of eco-innovation.
How Can Companies Implement Agile Supply Chain Practices Effectively?
Implementing agile supply chain practices requires a comprehensive strategy that combines innovative technology, cross-functional collaboration, and dynamic process optimization. Companies need to reengineer internal processes, integrate real-time analytics, and cultivate a flexible culture throughout the organization to reduce risks and continuously improve performance.
What Are the Steps to building an Agile and Responsive Supply Chain?
Building an agile supply chain involves several key steps: 1. Invest in technology infrastructure—such as cloud systems, IoT sensors, and AI analytics—to gain real-time data and forecasting capabilities. 2. Develop collaborative relationships with suppliers and logistics partners built on trust and data sharing. 3. Create cross-functional teams from procurement, operations, IT, and finance to enable rapid decision-making and execute contingency measures. 4. Conduct regular scenario planning and simulations to test the system’s responsiveness. 5. Continuously monitor performance and make iterative adjustments based on evolving market conditions and technological advancements.
These measures can improve response times by approximately 30% and significantly reduce downtime during disruptions.
How Do Cross-Functional Teams Enhance Supply Chain Agility?
Cross-functional teams break down departmental silos by bringing together expertise from operations, IT, procurement, finance, and sales. This collaborative approach leads to faster issue identification, better resource allocation, and more effective implementation of innovative solutions. When disruptions occur, these teams immediately assess financial and logistical impacts to coordinate a unified response, resulting in a supply chain that is both more resilient and adaptive. Research suggests that such collaboration can improve efficiency by around 25%.
What Metrics Measure the Success of Agile Supply Chains?
Success in agile supply chains is measured through both quantitative and qualitative metrics, including lead time reduction – Order fulfillment rates – Inventory turnover—cost savings – On-Time Delivery (OTD) – Cycle time reduction
Additional KPIs, such as customer satisfaction scores and the percentage of orders affected by disruptions, offer important feedback to further refine agile practices. Improvements in cycle times by 20–35% and increases in order accuracy by 15% or more are common outcomes of effective agile strategies.
What Are the Challenges and Solutions in Supply Chain Risk Management?
Global supply chains are complex, and common challenges include unforeseen disruptions, variable supplier reliability, regulatory compliance issues, and cyber risks. Successfully managing these risks requires a systematic approach, blending technology, strategic planning, and close collaboration with partners to identify and mitigate potential issues early.
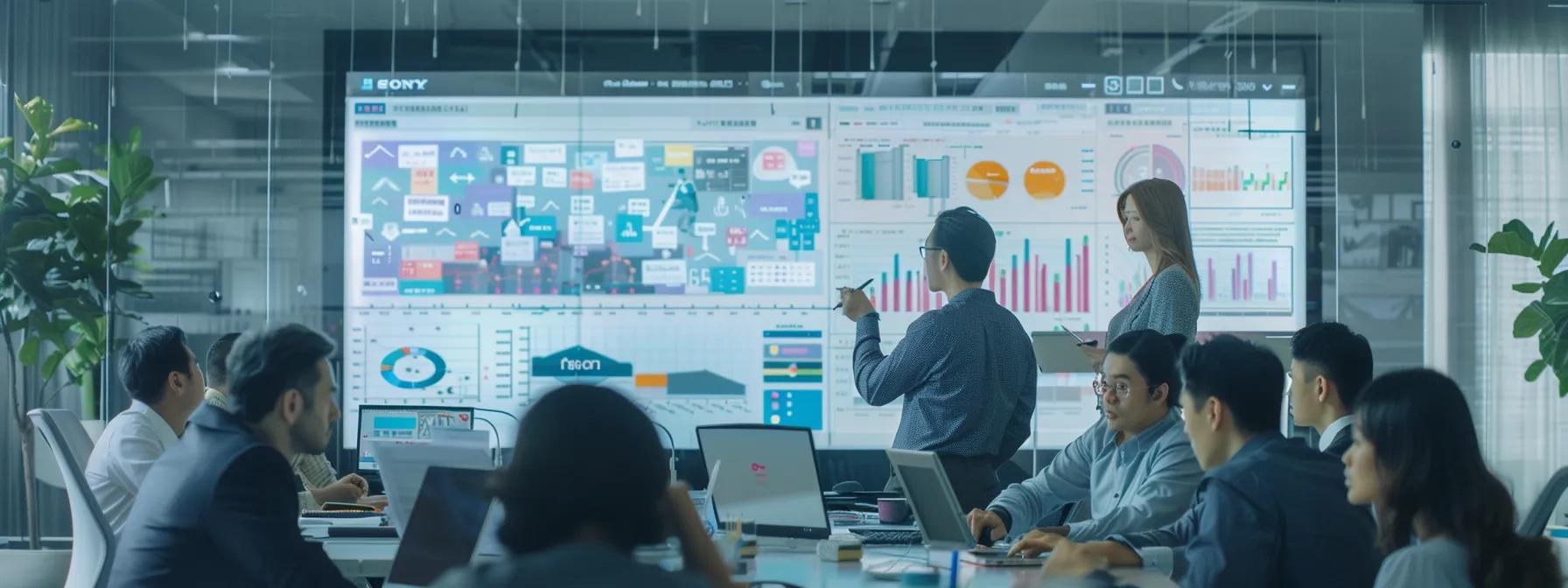
How Can Scenario Planning Mitigate Complex Supply Chain Risks?
Scenario planning allows companies to simulate various disruption scenarios—from natural disasters to economic shocks—and assess their impact on operations. Through these simulations, businesses develop tailored contingency plans, enabling faster and more effective responses when real disruptions occur. Research indicates that such planning can shorten response times by up to 40%, allowing leaders to preemptively adjust sourcing strategies and logistics plans.
What Are the Most Common Supply Chain Disruptions and How to Prepare?
Common disruptions include natural disasters, transportation delays, supplier insolvencies, cyberattacks, and sudden demand surges. To prepare, companies should diversify suppliers, maintain safety stocks, invest in real-time monitoring technology, and develop detailed contingency plans. Strategies like dual-sourcing for critical components and advanced logistics software can reduce disruptions by 25–30% through regular audits, drills, and continuous improvements.
How Does Collaboration With Partners Improve Risk Management?
Collaboration cultivates an ecosystem of shared data, resources, and contingency planning. By establishing trust-based relationships with suppliers, logistics providers, and even competitors, companies enable seamless information flow and early issue detection. Integrated digital platforms can trigger automated alerts for joint responses, and collaborative risk assessments can improve overall supply chain reliability by up to 20%.
How Do Leading Organizations Drive Supply Chain Resilience and Innovation?
Industry leaders drive resilience and innovation by adopting advanced technologies, implementing agile practices, and fostering a culture of continuous improvement. They invest heavily in digital transformation initiatives, employee training, and strategic partnerships to outperform competitors even during disruptions. Their experiences serve as valuable case studies for organizations seeking to enhance operations in a volatile global landscape.
What Lessons Can Be Learned From Top Consulting Firms?
Leading consulting firms demonstrate that integrating risk management with digital transformation is key to resilient supply chains. They advocate for comprehensive diagnostics, technology integration, and balanced scorecard approaches to measure performance metrics such as delivery speed, cost efficiency, and response agility. Case studies from firms like Deloitte and McKinsey show that proactive scenario planning and technology adoption can reduce disruption-related costs by around 30%. Continuous training and cross-functional integration are also critical for long-term success.
How Do Industry Events and Reports Influence Supply Chain Practices?
Industry events, conferences, and analytical reports provide essential forums for exchanging insights and benchmarking best practices. They alert companies to emerging risks and opportunities, allowing for early strategic adjustments. Reports such as the Gartner Supply Chain Top 25 highlight that investing in digital supply chain initiatives can boost operational resilience by up to 35%. These platforms help ensure that strategies remain current with global best practices.
What Role Do Supply Chain Leaders Play in Driving Change?
Supply chain leaders set strategic priorities, champion new technologies, and nurture a culture of continuous improvement. They align supply chain initiatives with broader business objectives and use data, industry benchmarks, and cross-functional collaboration to guide their decisions. Effective leadership, supported by ongoing training and transparent communication, results in faster adaptation to market changes and improved operational resilience.
Final Thoughts
Achieving supply chain resilience requires a multifaceted approach that integrates risk management, agile practices, advanced digital tools, and innovative logistics solutions. The strategies discussed—from real-time monitoring and predictive analytics to detailed scenario planning—highlight the importance of continuous improvement and preparedness in maintaining operational continuity. Companies that invest in technology, foster collaboration, and embrace proactive leadership are better positioned to reduce disruptions and drive performance improvements across diverse industries.
Frequently Asked Questions
Q: What exactly defines supply chain resilience? A: It is the ability of a supply chain to prepare for, respond to, and recover from disruptions through proactive risk management, flexible processes, diversified sourcing, and advanced digital tools.
Q: How does digital transformation impact supply chain performance? A: Digital transformation automates processes, provides real-time visibility, improves forecasting accuracy, and enables quicker decision-making—resulting in reduced costs and enhanced operational efficiency.
Q: Why is real-time monitoring critical in logistics? A: It enables businesses to track shipments, detect anomalies, and promptly address issues using IoT sensors and digital dashboards, thereby reducing delays and quality issues.
Q: Can agile supply chain practices really reduce downtime during disruptions? A: Yes, by enabling swift responses through cross-functional collaboration and rapid decision-making, agile practices can cut downtime by 30–40%.
Q: What benefits do integrated supply chain software solutions offer? A: They streamline operations, improve order accuracy, lower operating costs, reduce manual errors, and ensure faster response times through complete end-to-end visibility.
Q: How do cross-functional teams contribute to supply chain agility? A: They combine expertise from various departments to quickly identify issues, coordinate responses, optimize resources, and enhance overall responsiveness.
Q: What future trends are expected to shape supply chain resilience? A: Trends include greater adoption of AI and machine learning for predictive analytics, blockchain for transparency, increased integration of IoT devices, and more sustainable, eco-friendly logistics practices.